Cure Oven Equipment
- EVCO Engineered Solutions designs custom engineered solutions for your curing needs.
- Below are some different types of high ROI part curing systems we design.
- Don’t see a solution for your product? Contact us and let us know what you need!
- Don’t know what you need? Contact us for a free consultation!
Why is an engineered cure oven necessary for a quality finish? Check out our knowledge page to read more about the importance of well designed ovens.
Convection Oven – Passthrough
- Passthrough Layout:These ovens are designed for continuous curing, making them ideal for large-scale manufacturing and industrial applications where many parts need to be cured quickly. Parts are loaded onto a conveyor and move through the oven, reducing manual labor, improving efficiency and creating consistent results.
- Consistent Heat:Convection ovens heat the air surrounding the parts, which then heats the powder coating and the substrate evenly. This method allows for more consistent and deeper curing, ensuring a uniform finish and better adhesion across the entire part.
- Temperature Control:Convection ovens offer better control over the curing temperature and time, allowing for precise adjustments based on the part’s geometry and the type of powder coating used.
- Customizable size:These ovens are comprised of numerous splip together oven panels. Our engineers easily design nearly any shape to accodate the most efficent layout for your space.
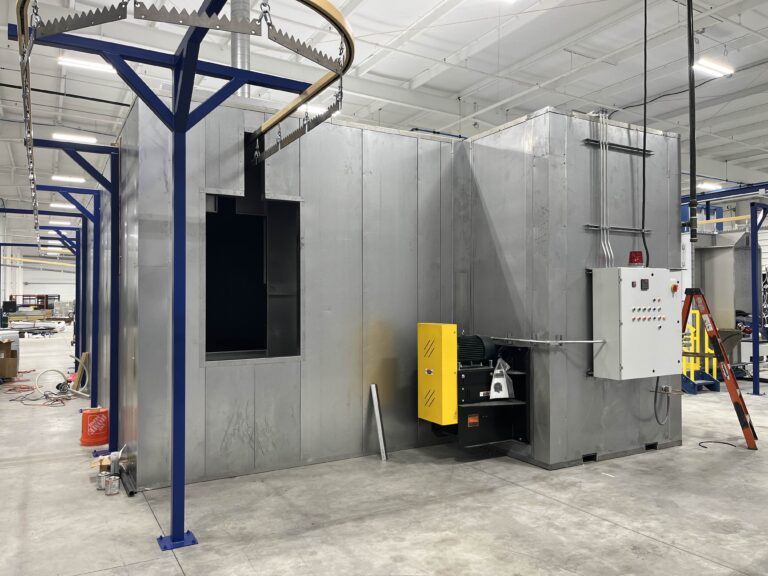
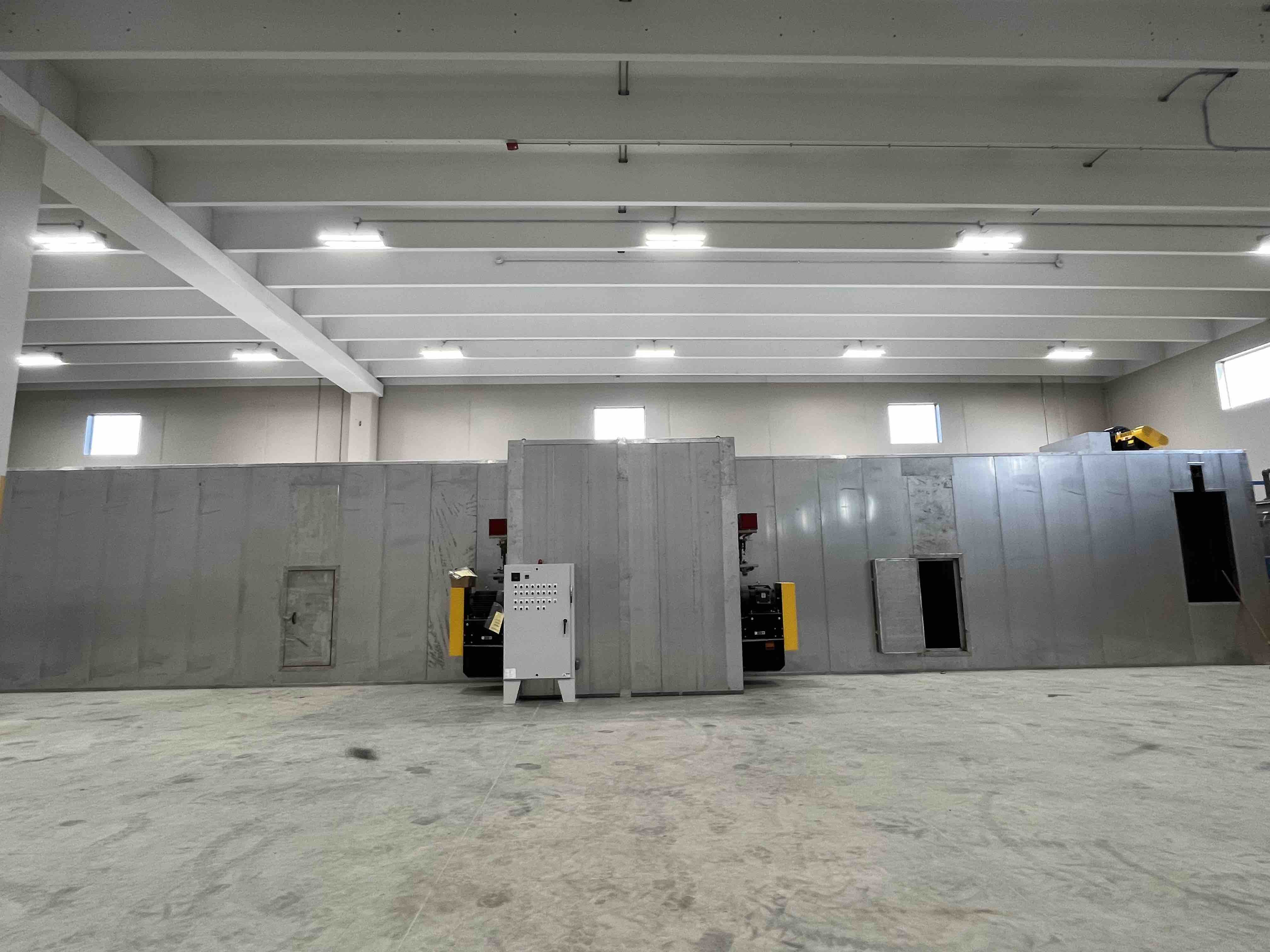
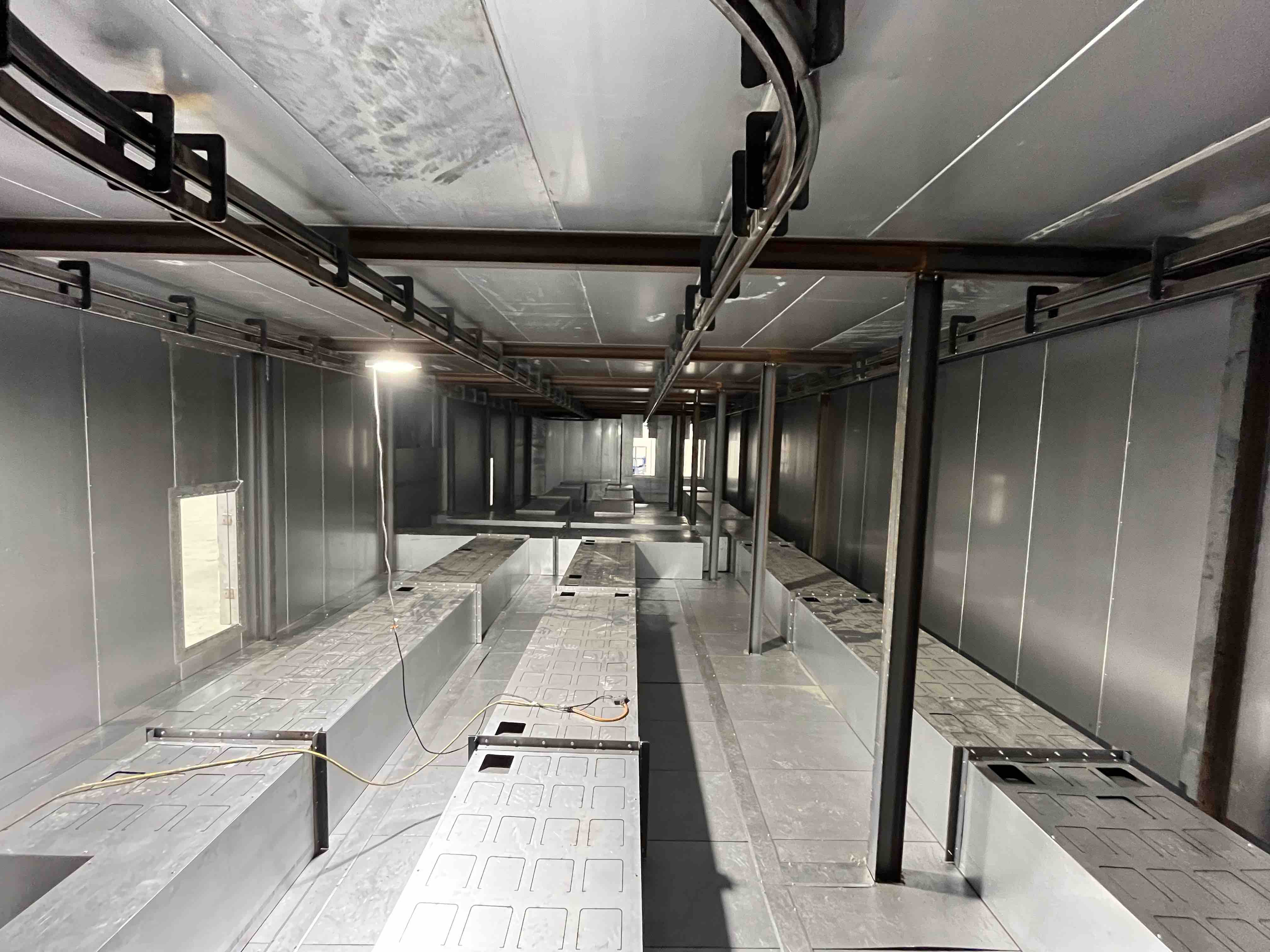

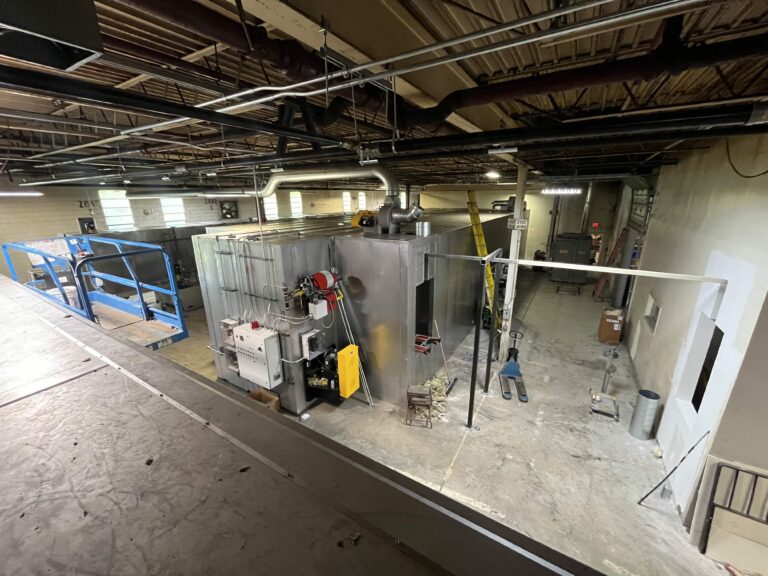
Convection Oven – Batch
- Batch Layout:These ovens are designed for batch curing, making them ideal for low to medium-scale manufacturing and industrial applications. Parts are loaded onto carts or more conveniently a manual overhead conveyor and parked in the oven. After cured the parts are removed and the next group, or batch, is put in.
- Consistent Heat:Convection ovens heat the air surrounding the parts, which then heats the powder coating and the substrate evenly. This method allows for more consistent and deeper curing, ensuring a uniform finish and better adhesion across the entire part.
- Temperature Control:Convection ovens offer better control over the curing temperature and time, allowing for precise adjustments based on the part’s geometry and the type of powder coating used.
- Customizable size:These ovens are comprised of numerous slip together oven panels. Our engineers easily design nearly any shape to accodate the most efficent layout for your space.
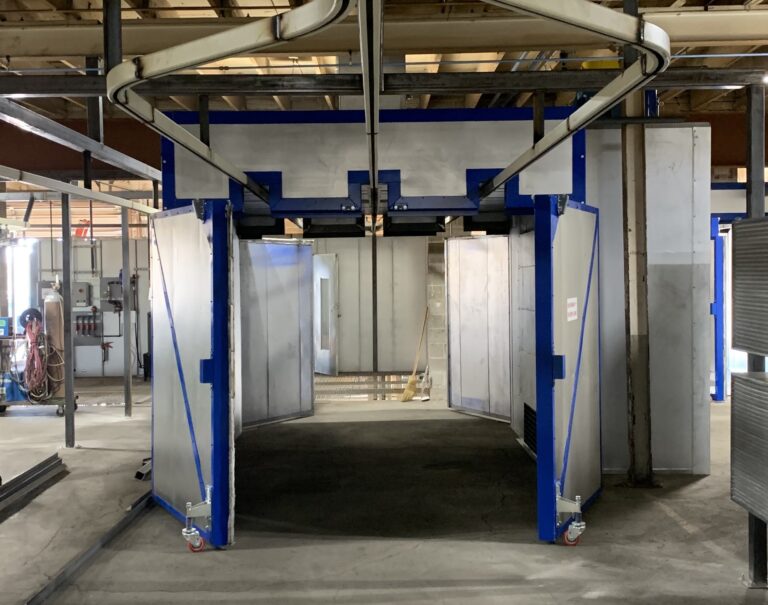
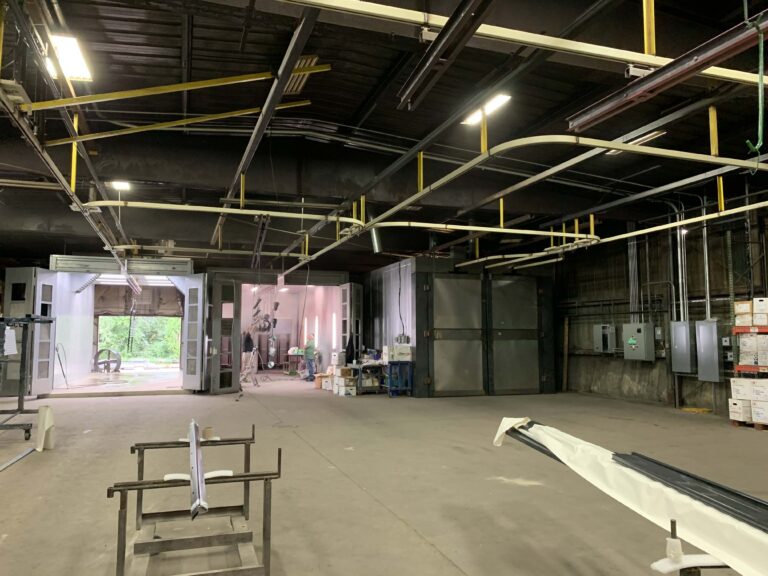
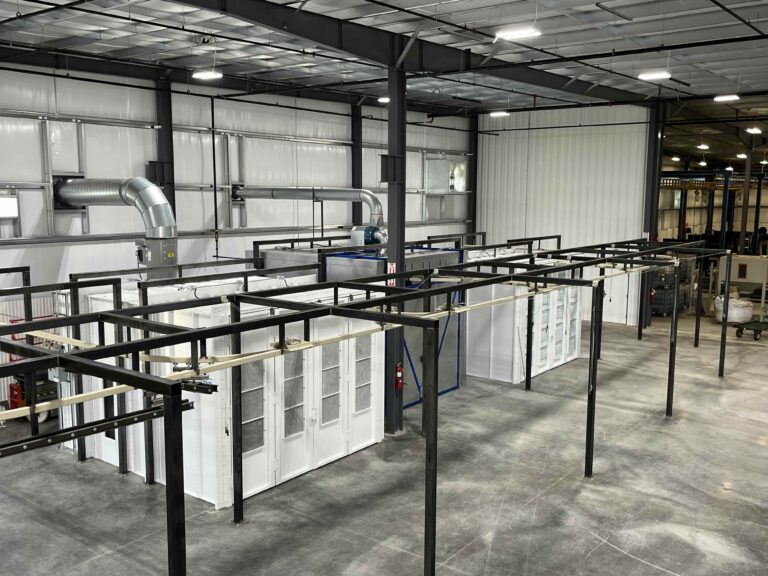
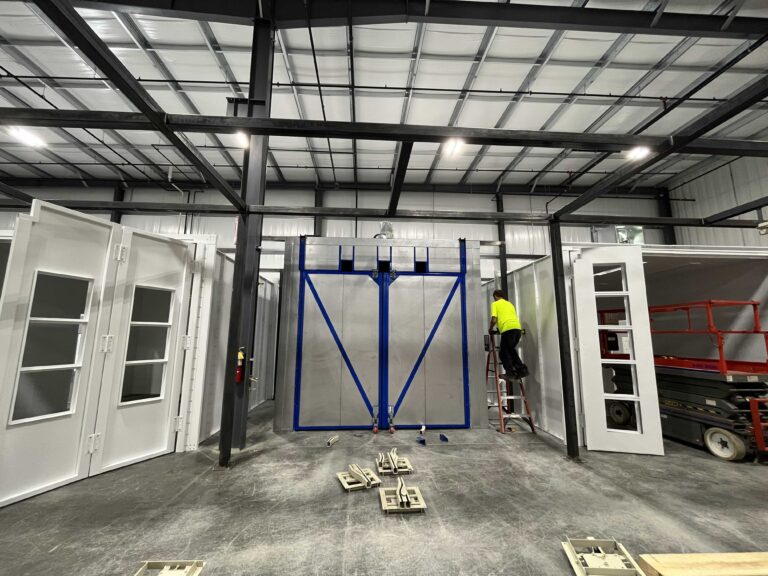
Infrared (IR) Ovens
- Line of Sight:
IR ovens rely on radiant energy, so a clear line of sight between the IR source and the coating surface is essential for effective curing. This feature makes them great at curing flat parts or parts with little geometry.
- Part Design:
Complex part shapes can pose challenges for IR curing, as the radiant energy may not reach all areas evenly.
- Conduction and Combination Systems:
Conduction (direct heating by contact) can be a powerful ally to any curing process. For parts with mostly flat surfaces and some complex areas we often pair IR and convection ovens to acheive faster and complete curing. These are called IR-enhanced convection ovens, which combine the benefits of both technologies for optimal performance.
- Shortwave vs. Mediumwave:
Shortwave IR ovens are used for quick, high-intensity cures, while mediumwave IR ovens are suitable for a wider range of applications.
- Gas Catalytic IR:Gas catalytic IR lamps are lest costly to operate (utility wise) than pure electric IR. Both IR systems can cure powder coatings in a third of the time of conventional baking, making them ideal for flat components like wall signs or art.
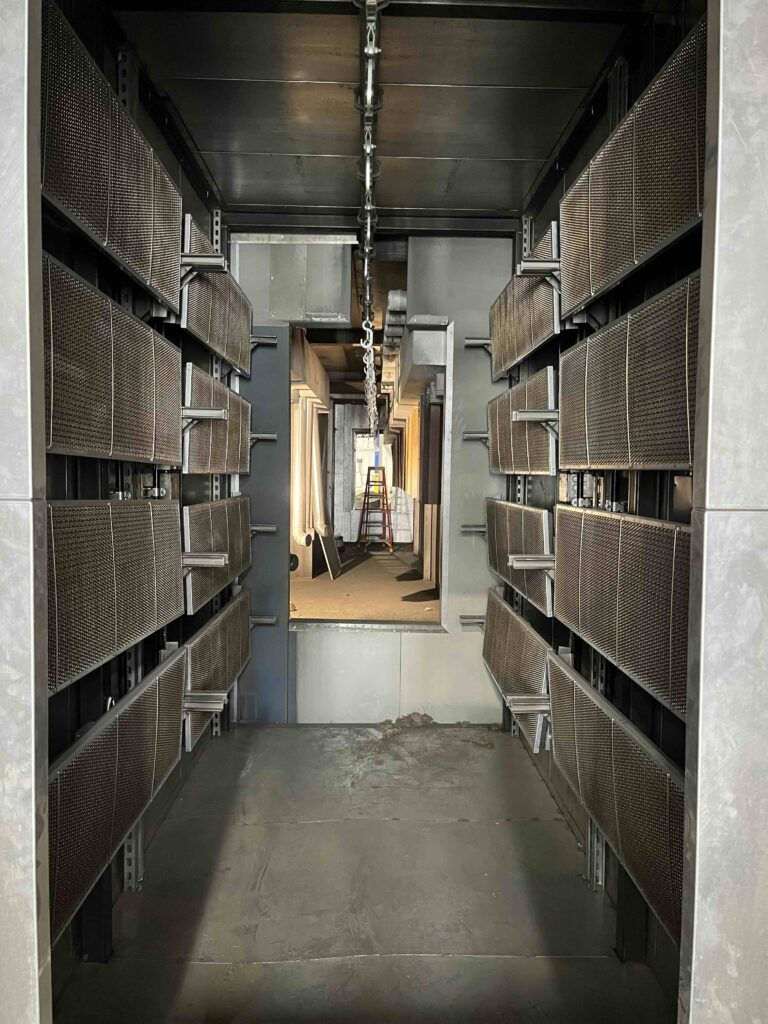
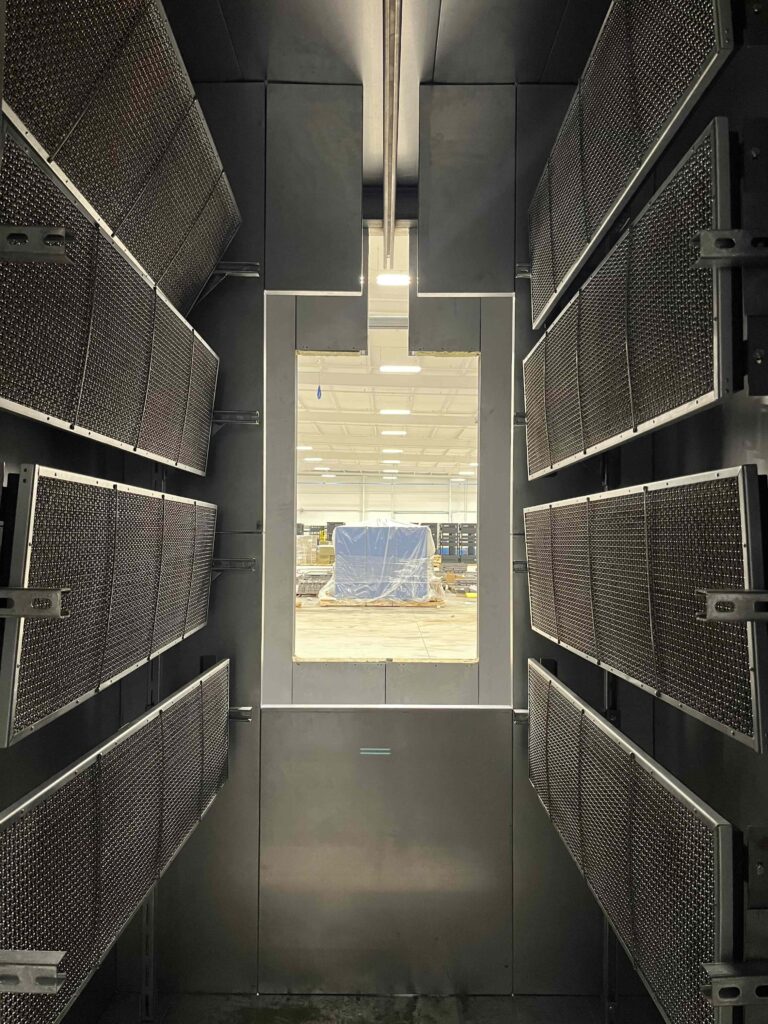
Heated Air-Makeup Cure Booths
- Simplicity and Cost effectiveness:
Manual spray booths with integrated heated air makeup are less complex and less expensive than automated systems, making them a practical choice for smaller throughput.
- Heated air makeup:
Heated air makeup allows for faster drying times than traditional room temp curing.
- Good for medium to low-volume painting:
They are well sited for painting small batches, individual parts or even inline with a slow moving conveyor.
- Space saving layout:
Manual booths with integrated cure rooms are excellent for saving space as they eliminate the need for separate cure rooms.
- Color Flexibility:
Spray and cure one part then immediately switch to another color with no down time or cleanup needed.
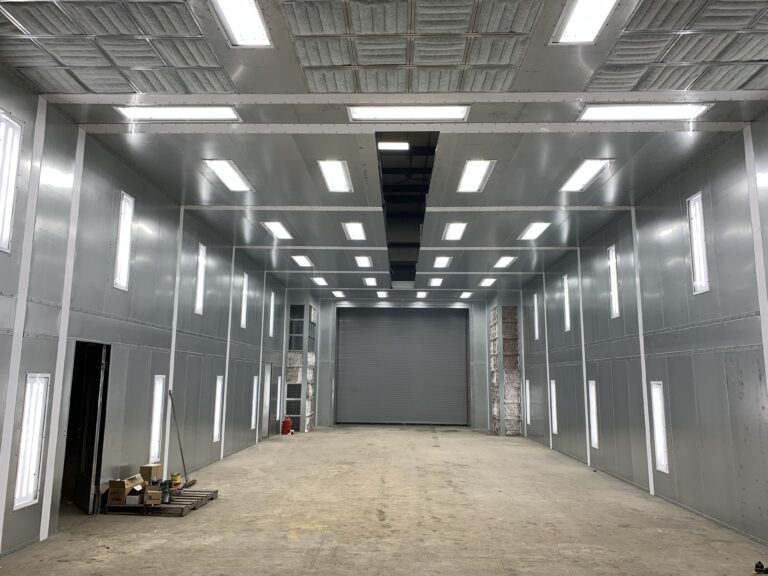
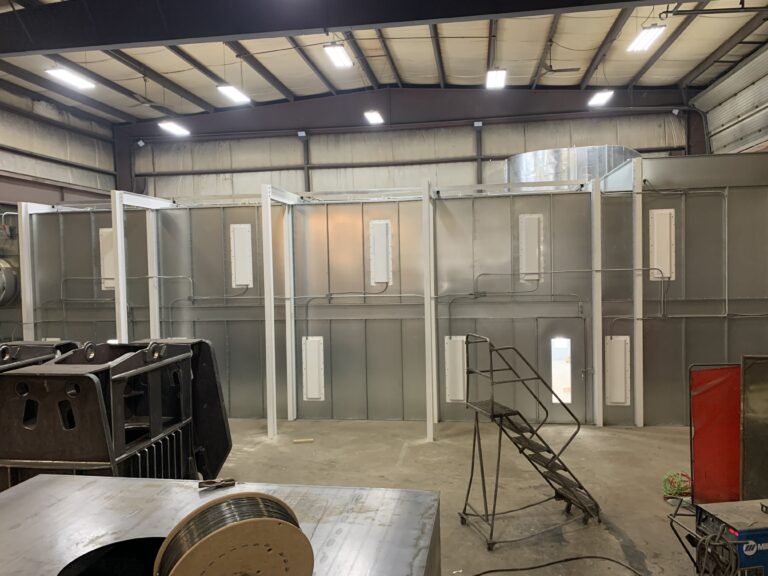